Modern technology enables an environmentally friendly circular economy: the bio-LNG from Darchau is used as lorry fuel. Many HEROSE valves are used in the liquefaction of the biogas and storage of the fuel.
It‘s whistling and hissing in the pipes – we are standing between the cold box and the large double-walled LNG storage tank. The lowing and occasional bellowing of the 1599 animals can be heard from the neighbouring barns. The liquid manure that one of these animals produces in 12 months, when turned into liquid bio-LNG, allows a gas-powered lorry to travel around 725 kilometres. In total, over 900 tonnes of bio-LNG are produced here every year.
Circular economy and a long added value chain
The Ruhe Group focusses on economy and ecology. The goal is innovative solutions and an optimised cirular economy. The result: Germany‘s first compact installation for the production of bio-LNG from biomethane located in Darchau on the Elbe floodplain and demonstrating that it works. Thanks to its many years of experience with biogas plants, the company has developed from an operator to a concept and component supplier and has become a plant constructor for methane liquefaction. Ruhe also offers the marketing of renewable gases, sustainability certification and maintenance services.
Bio-LNG –green fuel for the energy revolution
Darchau’s biogas plant supplies five combined heat and power plants with energy and produces cheap and sustainable electricity that is fed into the national grid. The heat that is generated supplies around 280 households and public facilities. Biogas can be used not only to generate electricity and heat, but also to produce fuel. The LNG liquefaction plant has been supplementing the existing biogas plant since October 2022. The micro-liquefaction technology produces with bio-LNG a clean, liquid fuel with zero emissions and a neutral carbon footprint, without the need to use expensive coolants such as nitrogen.
Cattle slurry and manure as an energy source
Part of the raw material for the biogas is produced naturally during cattle fattening – manure and slurry from the cattle contain a lot of energy. The six large barns house 1599 fattening bullocks. The animals arrive at the farm when they are 6 months old and weigh around 200 kilos; they stay for 12 months until they weigh over 750 kilos. Their waste products are transported underground by pipeline to the biogas plant. In order to extend the value chain, a meat factory of a regional butcher is attached, and this processes the high-quality meat. The majority of the cattle are slaughtered on a contract basis and marketed directly.
From the barn to the fermenter
The organic material is converted into methane in the two 5,000 cubic metre fermenters at around 40 degrees in the absence of air. The tanks are insulated and heated using electricity generated from renewable sources. The material is fed in and mixed via sliding floors and screws. Fermentation takes between 40 and 70 days – depending on the fermentation quantity and conditions. Due to the constant replenishment of the fermenters, a certain amount always overflows into the fermentation residue tanks. Depending on the time of year, the fermen-tation process continues there until the material has cooled down to below 30 °C.
In the three fermentation residue stores, each 10,000 cubic metres in size, what remains is what does not ferment: a lot of water and ligneous structures that cannot be converted into biogas by the bacteria. These residues are the best fertiliser for the meadows – better and more environmentally friendly than fresh manure, because there is no more methane outgassing in the fields. It is therefore a complete cycle: agriculture plus energy generation, which is 100 per cent powered by agricultural residues.
- At the storage tank for cryogenic liquefied CO2 as well as bio-LNG
- On pipelines between the liquefaction of the bio methane, the storage as well as the filling station
- On the storage tank for cryogenic liquefied CO2 and bio-LNG to set up safety valves
- For use when servicing safety valves
- Protection of pressurised tanks (storage of C02 and bio-LNG) and pipelines
- Pressure protection of the processes for separating methane and CO2 in membrane systems
- Controlling the bio-LNG flow in pipeline from the storage tank to the filling station unit as well as in the dispenser unit
- Expansion valve in the cold box for liquefying organic natural gas into bio-LNG
- In piping systems between liquefaction, storage and loading system
Turning manure into energy – biogas production
The resulting gas mixture consists of 52 per cent methane, 46 per cent CO₂ and accompanying substances such as oxygen and nitrogen. Hydrogen sulphide and water are removed through scrubbing. The gas is then channelled into the spur feeders – either to the combined heat and power plants in the region or to the new methane liquefaction plant. This is where the fine purification begins: In order to protect the treatment technology, the activated carbon filter removes fine sulphur particles and ammonia as well as some of the volatile organic carbons.
We process 100 % manure and slurry for the organic LNG – no renewable raw materials are used.
Florian Menke, Marketing Manager RUHE Biogas
Separating methane and CO₂
Methane and CO₂ are separated with the help of hollow fibre membranes. The gas is pressurised to 14 bar and passes through hollow fibre membranes – here the CO₂ diffuses faster and can be separated. The three-stage membrane process achieves a biomethane purity of over 98 per cent and significantly less methane is lost compared to the pressure swing adsorption.
Methane liquefaction then takes place in the so-called Cold Box. A compresor compresses the gas to over 100 bar. There are several Joule Thomsen valves in the Cold Box, in which part of the gas is always expanded. The cold from the resulting expansion is used to cool down the biomethane and finally liquefy it at –155 °C so that it can then be fed into the vacuum tank.
Clean energy thanks to bio-LNG
The double-walled 60 cubic metre storage tank has a usable capacity of 24 tonnes of LNG. Approximately every 8 days, a trailer collects 18 tonnes of bio-LNG and takes it to a filling station in Lehrte, where it is sold by the kilo as lorry fuel. Compared to one litre of diesel, one kilo of LNG has around 1.4 times the amount of energy. At the same time, a kilo of LNG is about as expensive as diesel fuel. Bio-LNG is not subsidised, it has to compete with diesel. The LNG fuelling station network in Germany is growing enormously. There are now around 160 refuelling stations, making us the leader in Europe.
Eleven liquefaction plants are currently being planned or realised – the concept works.
Justus Ruhe, Sales Engineer RUHE Biogas (not related to Kunibert Ruhe)
No exhaust gases thanks to CO₂ liquefaction
In a further process step, the CO₂ is to be converted into a liquid form – at around minus 25 °C. A connected dry ice plant is planned, which will produce dry ice pellets from the liquid CO₂. These pellets will then be used for cryo-cooling cargo in ports and at airports in the Hamburg area. In this way, the CO₂ bound in the process can also be used for an industrial purpose, thereby reducing fossil CO₂ in other processes. Carbon dioxide liquefaction is about to be commissioned.
Thinking the circular economy through
One of the Ruhe Group’s goals is to create a functioning circular economy with the longest possible added value chain. Bio-LNG is also used in the company’s own agricultural vehicles. The technology is available and a good proportion of heavy goods transport could be quickly and easily converted to the use of bio-LNG. The company is also in talks with manufacturers of agricultural machinery – the advantage of being both a manufacturer and user of environmentally friendly energy is obvious. At Ruhe, the aim is to cover everything that is possible with co-products. Other ideas and innovations could complement the plants, whether hydrogen or bio-methanol: from the plant to the animal and back to the field – generating green energy in the process and using it yourself, thinking through the added value chain to the end. An exciting concept, made possible by state-of-the-art technology.
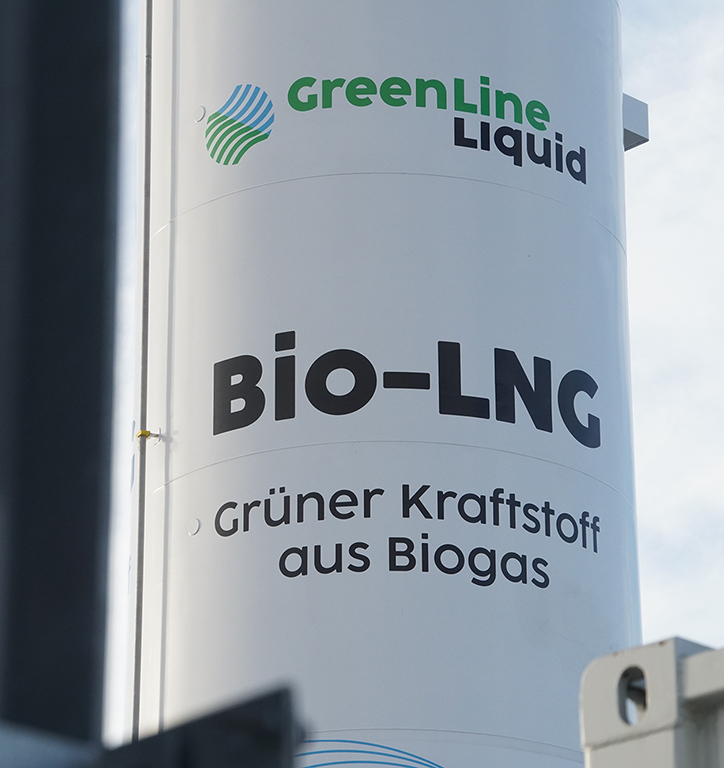
Ruhe Group
Company founder Kunibert Ruhe, a trained master farmer, is a pioneer in the biogas sector in Germany. Today, Ruhe Biogas Service GmbH is managed by his son Maximilian Ruhe. The group of companies focuses on sustainable agriculture and modern technology for an optimised circular economy. The innovative family business works together with research institutes and universities.